What Type Of Caster Wheels Should Industries Use?
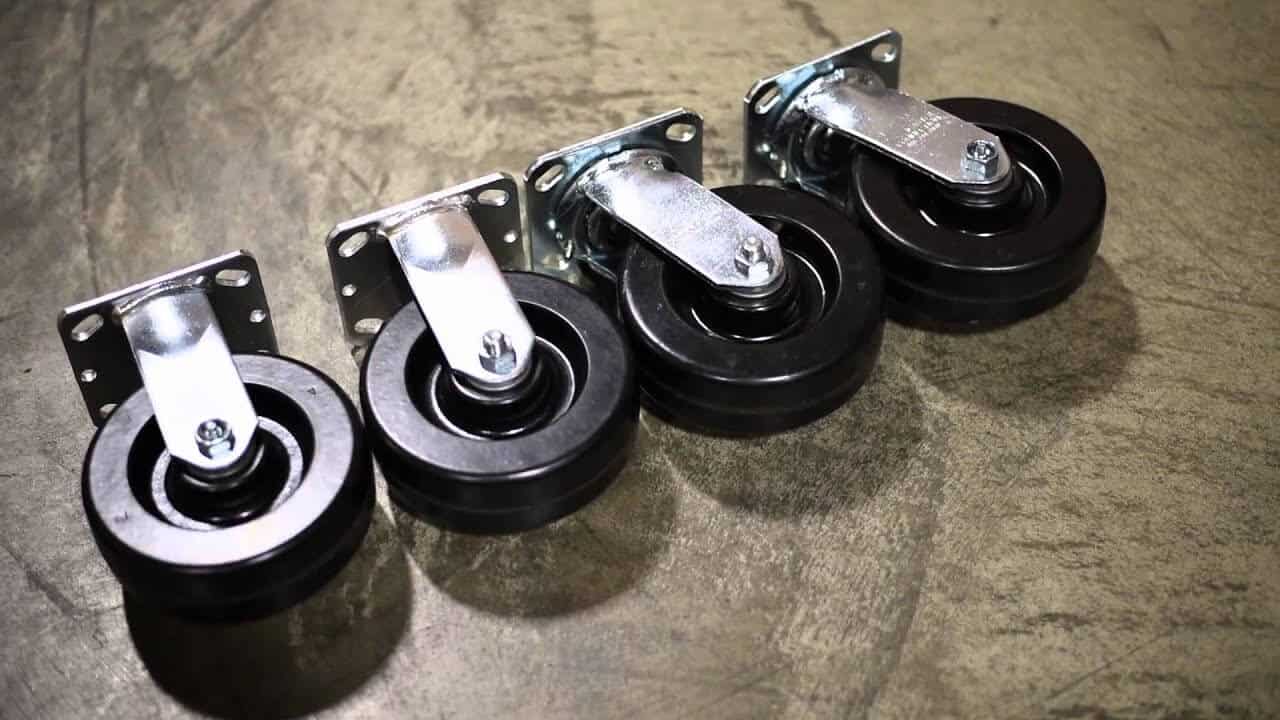
Choosing the right type of caster wheels for your industry is important, not only because it is important to the safety of your employees and the equipment but also because it is important for the longevity of the equipment. The industrial wheels come in different forms, such as Heavy-duty, Swivel, and Impact loading and brinelling.
Swivel Casters
Whether you need to move equipment or machinery, swivel caster wheels provide the speed and ease of movement you need. Swivel casters are also ideal for heavy-duty environments. Using swivel wheels increases your mobility while reducing your risk of injuries.
These wheels can reduce push/pull forces by up to 35-50%. They offer superior capacity and can be customized to fit your needs. In addition, these wheels can be customized for different floor types. Soft floorings require softer wheel materials. Harder floorings can handle harder wheel materials.
Heavy-Duty Casters
Whether you are looking for casters for a manufacturing plant, an aircraft assembly plant, or a warehouse, heavy-duty caster wheels are essential for the job. They are designed to be strong, durable, and affordable.
Unlike traditional wheels, heavy-duty caster wheels are built to withstand the weight of large workpieces and assemblies. They are used in manufacturing plants, warehouses, and distribution centers. They also allow for easier maneuvering of doors, carts, and containers.
Casters are made of gray iron castings. The wheels are inserted into a steel axle and attached with a bolt head. They are then treated in heat to prevent brinelling. The next machining process is the extrusion of the wheel material.
The wheels have a tread, or a groove, to help guide the load. This design helps ensure the proper weight distribution per wheel.
The material of the wheels also has an impact on the load capacity. For example, rubber and plastic wheels work well for lighter loads. Glass-filled nylon wheels can operate in harsh environments. They can withstand a temperature range of 550degF and up and can be used in an oily and greasy environment.
Impact Loading and Brinelling
Choosing the right caster wheel is important to ensure smooth and reliable performance. Casters are used to transport a variety of different equipment. Whether moving a piece of furniture, a patient’s bed, or an electronic device, you must be sure that you have the right wheel. The impact loading and brinelling of caster wheels are important to consider.
Impact loading occurs when a caster or wheel experiences a sudden, high-impact force. When this happens, the caster or wheel may break. This type of loading is typically caused by a high load placed on the caster while not in motion. This load usually causes a peak g-force, which can exceed the caster’s load capacity.
In some cases, this impact load can also cause a permanent deformity. This can include cracks or chipping. If the caster or wheel is made of a soft material, the impact load can cause the material to break off.
Materials Used to Make Caster Wheels
Depending on the application’s requirements, many different types of materials are used to make caster wheels. These include nylons, steel, elastomers, cast iron, and polyurethane. These materials have different properties, making them ideal for specific applications.
Polyurethane caster wheels are durable and easy to roll. They are resistant to abrasion, breakage, and cracking and are ideal for applications that require high performance. They are also non-marking and resistant to oils and chemicals. They are easy to push and are suitable for use on tow lines.
Pneumatic caster wheels are designed to be non-flat and provide cushioning. They can operate in various conditions, including wet and oily environments. These wheels are also resistant to chemicals. They are commonly used in manufacturing and warehouse environments. They also have high resistance to oil and grease. They do not go flat when they are used in high-traffic environments.
Soft-treaded caster wheels are used in processing plants and hospitals. They are made of thermoplastic elastomers and have a rubber edge that absorbs shock. They reduce noise and protect delicate floors.