Basic Hydraulics: An Interesting Overview For The Curious
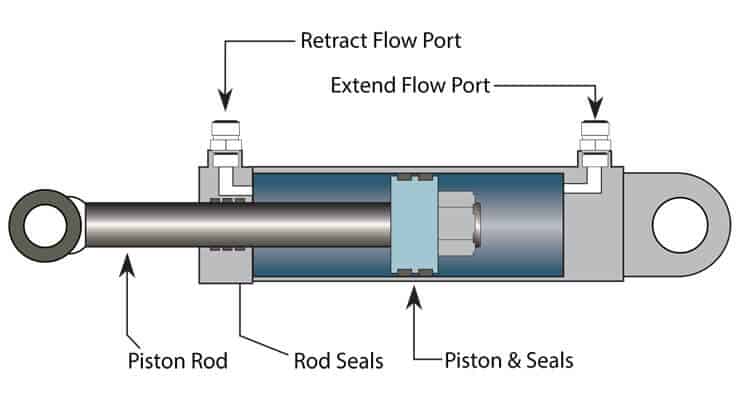
The use of hydraulics is common in construction equipment, farm implements, pumps, rams, and other industrial applications. These systems use a compressible fluid to transmit great amounts of force from one point to another. They are typically more durable and capable of providing greater power than electric or other comparable systems. In order to design or troubleshoot one, a person needs to have some basic understanding of their operation. Learn more about basic hydraulics below!
Basic Hydraulics: Elements Of A Common Hydraulic System
A hydraulic system is a relatively simple mechanism consisting of just a few main components. There are other subcomponents and accessories that are necessary for operation, but for the most part, they contain these items:
- Hydraulic fluid – this is a specialized oil that makes the whole system capable of operating.
- Reservoir – a place that holds the oil, not under pressure
- Pump – this then takes the fluid from the reservoir into the cylinder.
- Hoses – offer a means of transport for the fluid between all the other components.
- Cylinder – it is where the pressurized fluid is converted and provides the work.
While all of the above parts are critical to the system operating as intended, the hydraulic cylinder is the mechanism that converts the fluid energy into force. It is critical to achieving the desired end result in any hydraulic system. It’s basically, the main component without which, the job cannot be done.
Key Specifications Of A Cylinder
When designing a hydraulic system, consideration should be given to the construction of the cylinder itself. If this is overlooked the results may fall well short of expectations, or worse, it could result in a complete system failure. At a minimum, you need to think these five aspects though before you buy a cylinder for any application:
- The conditions it will be operating in. Not all cylinders can withstand the same amount of pressure, so this limit needs to be established. Also, you might need special components if you plan to use it in a harsh or adverse environment.
- The type of cylinder. The most common are tie-rod and welded. There are also classifications within those such as single-actuating and double-actuating. Basically, depending on the job it needs to get done, the type of cylinder used will differ.
- Bore size. This is basically the inner diameter of the cylinder housing. In general, larger bore sizes can generate more force but also cannot operate as fast as smaller ones. So, on one hand you get more force, but a slower work speed, while for weaker force you get faster speeds. Again, depending on the type of work you need to get done, you will choose the bore size accordingly.
- Stroke length, is basically the amount that the piston rod can travel within the cylinder.
- Piston rod. This is what moves back and forth within the cylinder during each stroke. You get to determine its size only after you decide on the bore size and stroke length.
As you can tell, hydraulic systems can be quite simple and easy to understand. The type of system you need will vary depending on the type of job, external conditions, and speed. With that being said, we hope our short article on basic hydraulic systems will be useful to you.